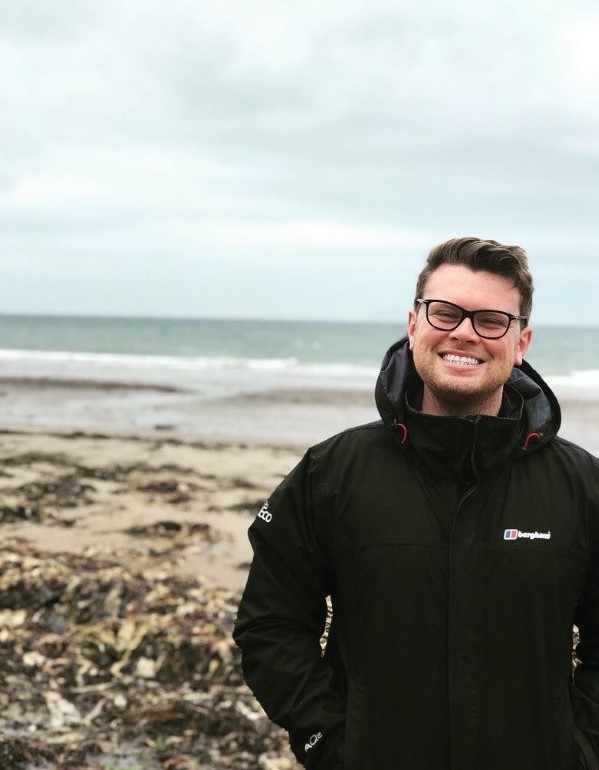
It often surprises people when I say the most challenging part of my role as Equipment & Maintenance Superintendent is managing CleanTreat® system changeouts. Our technology has a finite capacity before it needs to be replaced. Many people think a system changeout is as simple as emptying their vacuum hoover. However, the changeouts I manage are much more complex, taking weeks to plan and prepare and several days to complete. In addition to managing these changeouts, much of my role is also spent working on reducing this time, taking on the lessons and experience that each changeout provides.
What is CleanTreat® and how does it work?
CleanTreat® is a specialist water purification system and the first of its kind to be used in the aquaculture industry. CleanTreat® removes sea lice medicines from treatment water, allowing purified water to be returned to the sea. Our CleanTreat® systems are installed on dedicated offshore supply vessels, which sail to remote locations to ensure the safe handling of treatment water at fish farms.
The CleanTreat® process is designed to purify water continuously until the system has reached its operational capacity, at which point a changeout is required. This is assessed by routine sampling and analytical monitoring via high-performance liquid chromatography (HPLC). The changeouts take place roughly every two months for both of Benchmark’s CleanTreat® vessels.
The CleanTreat® vessels play a key role in supporting the use of our medicine, Ectosan® Vet, therefore, it is crucial that any operational downtime is kept to a minimum.
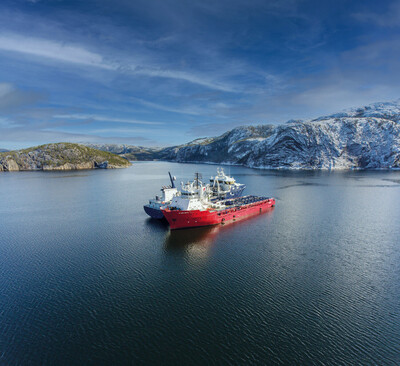
What is the agreed process for a CleanTreat® changeout?
Three to four weeks before changeout:
· First, I contact suppliers, preparing for multiple locations or last-minute changes in location, ensuring sites have suitable infrastructure.
· Next, I develop our technical stop plan, where teams meet to go through all risk assessments, the scope of work and timelines. After this, we have weekly update meetings with everyone involved.
There are a lot of steps involved in a CleanTreat® changeout. We also need to manage the organic material, plus maintenance of the UV filter and the vessel in general.
What makes a CleanTreat® changeout so challenging?
Location: The vessels are on active duty and sail to wherever they are needed to support treatments. This means changeout locations cannot be confirmed well in advance, and often occur in remote Norwegian fjords. This comes with additional risks of extreme weather and other logistical challenges, such as road access. This requires rigorous preparation with internal and external teams and an excellent understanding of what’s required and who is responsible for what activity, regardless of location.
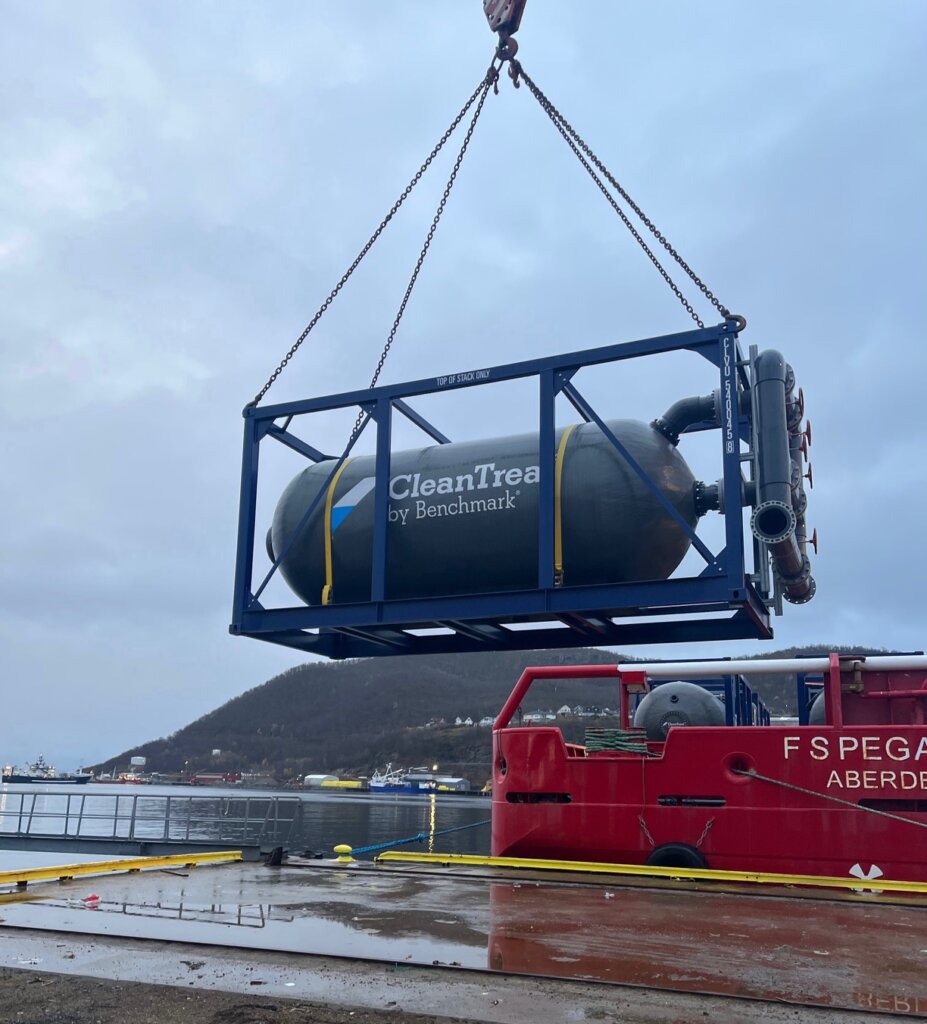
Specialist equipment: When changing out, the crew are working at height and lifting large pieces of equipment, requiring massive shoreside cranes.
In addition, we need access to industrial cleaning services, forklifts and manpower during the changeout. In order to complete the changeout safely, we always need to find a suitable location, with the right specialist infrastructure either onsite or the ability to bring to location.
Working conditions: The teams need to be able to handle confined spaces to empty, clean and disinfect our equipment onsite. We have strict safety measures for working with chemicals and work 24/7 and in all weather conditions, requiring expert training and highly procedural activities.
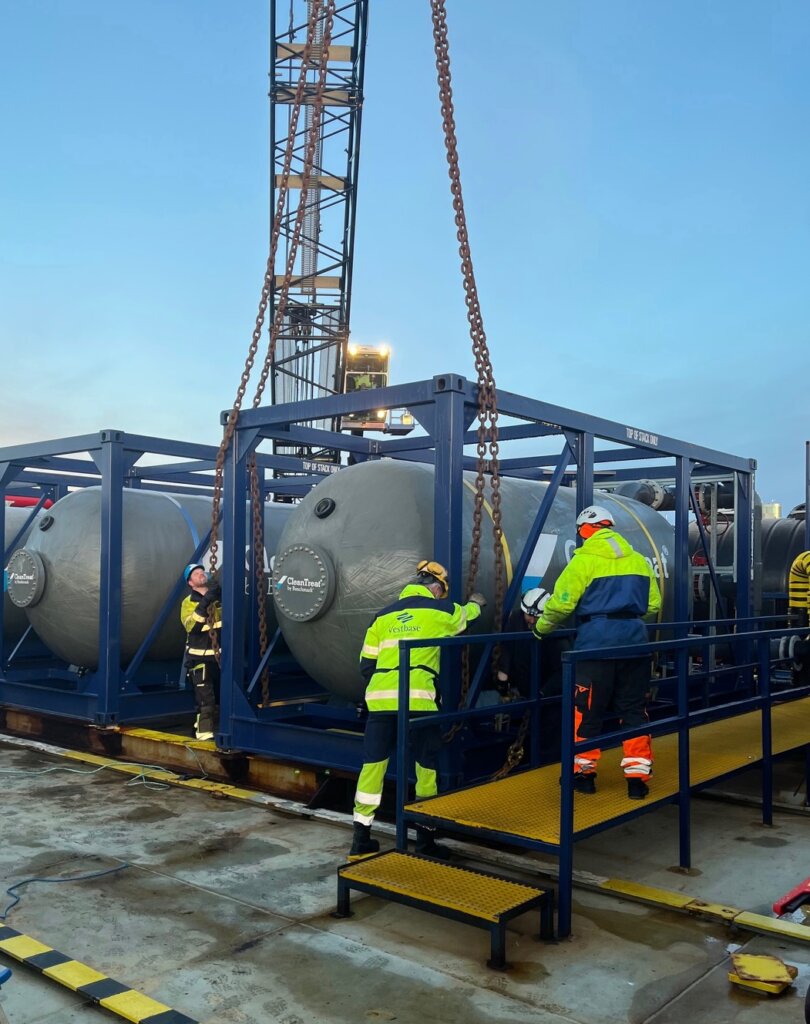
Expert team required: The whole process involves up to 30 people, both on location and providing off location support and planning, working in 12-hour shifts for several days. This includes experts
from Benchmark, the vessel provider, industrial cleaning team and the offshore base. Due to the remote and changing locations, we often have a different team and contractors for each changeout. Every team member needs proper training and every location needs a full risk assessment.
The importance of learning and improving
Through process and design optimisation, we have doubled the volume of water which can be purified by our systems before changeouts are required, reducing the changeout frequency and minimising the downtime for our customers.
Improvements to the system have included pre-filter installations (removing smaller particulate matter allowing more efficient uptake of the medicinal molecule), boost pumps (reducing overall pressure on the system) and modifications to our original system (allowing more effective distribution of water). Although not the only improvements we have made to the system over the years, these modifications have positively impacted the downtime associated with changeouts.
Despite the many challenges, I love working on this technology. CleanTreat® is driving sustainable practices in aquaculture, enabling fish farmers to use medicines in a responsible way. I’m proud of the role I play in #SolvingSeaLice.